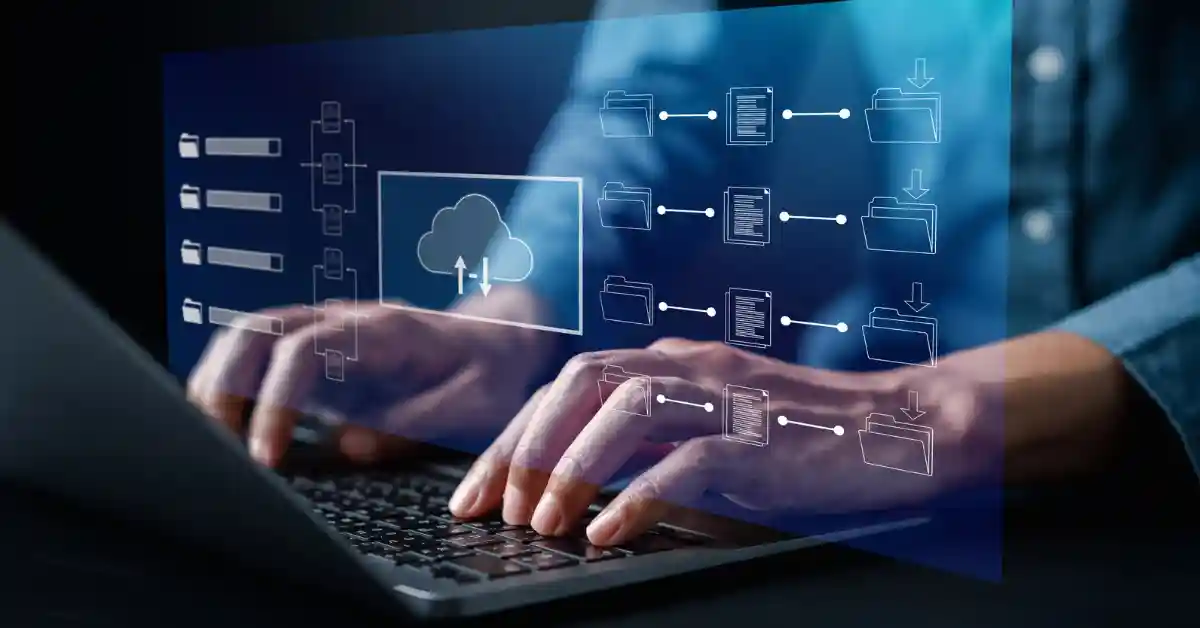
Order management becomes seamless with a work order system, designed to streamline your operations and enhance productivity. When you implement such a system, you gain the ability to track tasks, monitor progress, and allocate resources efficiently. This not only reduces downtime and minimizes errors but also improves communication among your teams. By leveraging a work order system, you ensure that every job is completed on time and to the highest standards, ultimately driving your success forward.
Overview of Work Order Systems
While many businesses rely on organized processes to manage tasks, a work order system streamlines operations by facilitating the creation, tracking, and completion of work orders. This system enhances productivity, communication, and compliance, ultimately leading to improved operational efficiency.
Definition and Purpose
The system is a work order software tool designed to manage and automate maintenance and repair tasks within an organization. Its primary purpose is to ensure that tasks are completed efficiently, enabling better resource management and enhancing service delivery.
Key Features
Definition of a successful work order system includes functionalities that cater to a diverse range of organizational needs. Key features typically include:
- Create work orders seamlessly
- Track progress in real-time
- Prioritize tasks based on urgency
- Assign personnel to specific work orders
- Attach documentation and photos
- Schedule maintenance and inspections
- Report on work order history and performance
The features not only simplify the work order process but also improve transparency and accountability within your team.
At its core, a work order management system enhances operational aspects by providing an organized framework for task management. Key features that contribute to its effectiveness include:
- User-friendly interface
- Integration with existing software
- Mobile access for on-the-go updates
- Automated notifications for task updates
- Analytics for performance insights
The implementation of these features ensures that you have a comprehensive tool to manage your workflow efficiently.
Types of Work Order Systems
Assuming you are exploring various options for a work order system, it’s important to identify the suitable type for your needs. These can be broadly categorized as follows:
Manual Systems | Traditional and paper-based processes for tracking work orders. |
Automated Systems | Web-based software solutions that streamline work order management. |
Mobile Work Order Systems | Apps that enable field technicians to access and manage work orders on-the-go. |
Cloud-Based Systems | Remote access to work order management through cloud technology. |
Custom Systems | Tailored solutions designed according to specific organizational needs. |
Perceiving the characteristics of these systems will help you select the best fit for your organization’s requirements.
Manual vs. Automated Systems
By evaluating manual and automated systems, you can discern which approach suits your operational workflow. Manual systems might seem cost-effective initially, but they often lead to inefficiencies and errors over time. On the other hand, automated systems provide real-time updates, error reduction, and improved tracking capabilities, ensuring your work orders are managed more effectively.
Industry-specific Applications
Among work order systems, industry-specific applications are designed to cater to the unique demands of various sectors. Each industry, from manufacturing to healthcare, has distinct requirements for work order management. These systems streamline operations, ensuring compliance and efficiency tailored to your field.
Also, focusing on industry-specific applications allows you to utilize tools that enhance productivity and ensure safety. For instance, in healthcare, these systems manage urgent maintenance requests for critical equipment, which is vital for patient care. Meanwhile, in manufacturing, they can monitor machine performance and schedule preventive maintenance, ultimately reducing downtime. Adaptability and functionality in your work orders ensure an aligned approach to your industry's specific demands.
Benefits of Implementing a Work Order System
Clearly, adopting a work order system can significantly elevate your organization's performance. This structured approach to managing tasks leads to optimized resource allocation and streamlined communication, ultimately resulting in greater productivity and reduced operational costs. By centralizing work requests, tracking job statuses, and documenting processes, you can ensure that your team remains focused and engaged, paving the way for enhanced service delivery and customer satisfaction.
Improved Efficiency
Improved efficiency is a direct outcome of implementing a work order system. By automating routine tasks and standardizing procedures, you can minimize the time spent on manual processes. This allows your team to concentrate on high-priority assignments, while the system arranges and prioritizes tasks, creating a more organized workflow. As a result, your project completion rates rise and resources are utilized more effectively.
Enhanced Accountability
Implementing a work order system brings about enhanced accountability within your team. By clearly defining roles and responsibilities, you foster an environment where each team member understands their obligations. This transparency minimizes confusion and reduces the likelihood of errors, as individuals can readily track their progress and that of their colleagues. With documented workflows and performance metrics, you'll be able to identify areas for improvement and celebrate successes.
Due to the enhanced accountability provided by a work order ticket system, your organization can achieve much higher standards of reliability and performance. When team members are aware of their tasks and the timelines for completion, they are more likely to meet expectations, reducing the risk of missed deadlines or overlooked responsibilities. Furthermore, regular monitoring of performance metrics allows you to spot trends, address issues proactively, and recognize individual contributions. This not only boosts morale but also fosters a culture of ownership and commitment throughout your organization.
Best Practices for Setting Up a Work Order System
To establish an effective work order system, you must focus on user-friendly design, seamless integration with existing tools, and clear processes. Prioritize automation features to reduce manual input and explore customizable options tailored to your organization’s unique workflow. Regularly review and adjust your system based on user feedback and evolving organizational needs to ensure it remains efficient and relevant.
Assessing Organizational Needs
Practices for assessing your organization's needs involve identifying the specific requirements of different departments and understanding their workflows. Discuss with team members to pinpoint pain points and gather input on desired features. This comprehensive evaluation not only helps in selecting the right work order system but also promotes user engagement and support during implementation.
Training and Support
By providing comprehensive training and ongoing support, you can ensure a smooth transition to a new work order management system. Training sessions should be tailored to various user roles, emphasizing practical application and system features.
For instance, offering hands-on workshops and easily accessible online resources can significantly boost your team's confidence in using the system. Regular check-ins and the establishment of a dedicated support team will foster a sense of security among users, enabling them to overcome challenges quickly. Furthermore, emphasizing the benefits of the system can create a positive culture around its use, making everyone feel empowered and engaged in their tasks.
Common Challenges and Solutions
Your organization may face several challenges when implementing a work order system, including resistance to change and integration with existing systems. Understanding these challenges allows you to proactively address them, paving the way for a smoother transition and improved operational efficiency.
Resistance to Change
Among the most significant hurdles you may encounter is resistance to change from your team. This often stems from a fear of the unknown and concerns over adapting to new technology. To combat this, it’s necessary to foster open communication, offer comprehensive training, and emphasize the long-term benefits to ensure buy-in from all stakeholders.
Integration with Existing Systems
The integration of your new work order system with existing systems can also present significant obstacles. You need a strategic approach to ensure a seamless transition and functionality across platforms.
It is imperative to assess your current systems thoroughly and identify any potential compatibility issues early in the process. A well-thought-out integration plan can help mitigate risks associated with data loss or disruption in operations. Engaging with IT professionals who have experience in system integration can facilitate smooth transitions, ultimately enhancing efficiency and productivity in your organization.
Future Trends in Work Order Systems
The future will see a significant shift towards increased automation and enhanced data analytics. These advanced systems will not only streamline processes but also provide valuable insights, allowing you to make informed decisions quicker. As organizations adopt these innovative technologies, your ability to manage work effectively will vastly improve, ultimately leading to increased productivity and better resource allocation.
Technological Advancements
By leveraging emerging technologies such as artificial intelligence, machine learning, and the Internet of Things, you can expect a more efficient work order system. These advancements will simplify communication, optimize workflows, and offer real-time visibility into your operations, empowering you to manage tasks effortlessly.
Predictive Maintenance
Trends indicate that predictive maintenance will play a pivotal role in the evolution of work order ticket systems. By incorporating data analytics and IoT capabilities, these systems will allow you to anticipate equipment failures and address issues proactively, significantly reducing downtime and maintenance costs.
Also, utilizing predictive maintenance transforms your approach to equipment management. It shifts the focus from reactive repairs to proactive measures, enabling you to identify patterns that signal potential failures. Through continuous monitoring and analysis, you can enhance the lifespan of your assets, optimize resource allocation, and improve safety. This method not only saves you money by avoiding unexpected breakdowns but also ensures that your teams can operate at peak efficiency with minimal disruptions.
FAQ
Q: What is a work order system?
A: It is a management tool used by organizations to track, manage, and fulfill maintenance or service requests. It facilitates the creation, assignment, and monitoring of work orders, ensuring that tasks are completed efficiently and in a timely manner. This system can be utilized in various industries, including manufacturing, facilities management, and service-oriented businesses.
Q: How does a work order system improve efficiency?
A: Enhances efficiency by streamlining the process of task assignment and tracking. It minimizes the time spent on manual paperwork, reduces the risk of miscommunication, and enables teams to prioritize work based on urgency or importance. Additionally, with real-time updates and monitoring capabilities, managers can easily assess workloads and allocate resources more effectively.
Q: What features should I look for in a work order system?
A: Consider features such as user-friendly interfaces, mobile accessibility, automated notifications, reporting capabilities, task prioritization, and integration with other management tools or software. These features help ensure that the system meets your specific operational needs and enhances overall productivity.
Q: Can a work order tracking system be customized for different industries?
A: Yes, many work order tracking systems offer customization options to cater to the unique requirements of different industries. This may include specialized workflows, reporting formats, and field-specific terminology. Customizable work order systems ensure that organizations can tailor the platform to better align with their processes and improve user adoption.
Q: How can I measure the effectiveness of a work order management system?
A: The effectiveness can be assessed through various metrics, such as completion times for work orders, user satisfaction levels, and the number of completed tasks over a specific timeframe. Additionally, tracking improvements in response times and reduced downtime can provide insights into how well the system is functioning. Regular reviews and feedback from users can also help identify areas for enhancement and ensure optimal utilization of the system.